From Concept to Reality: How Custom LCD Designs Are Brought to Life
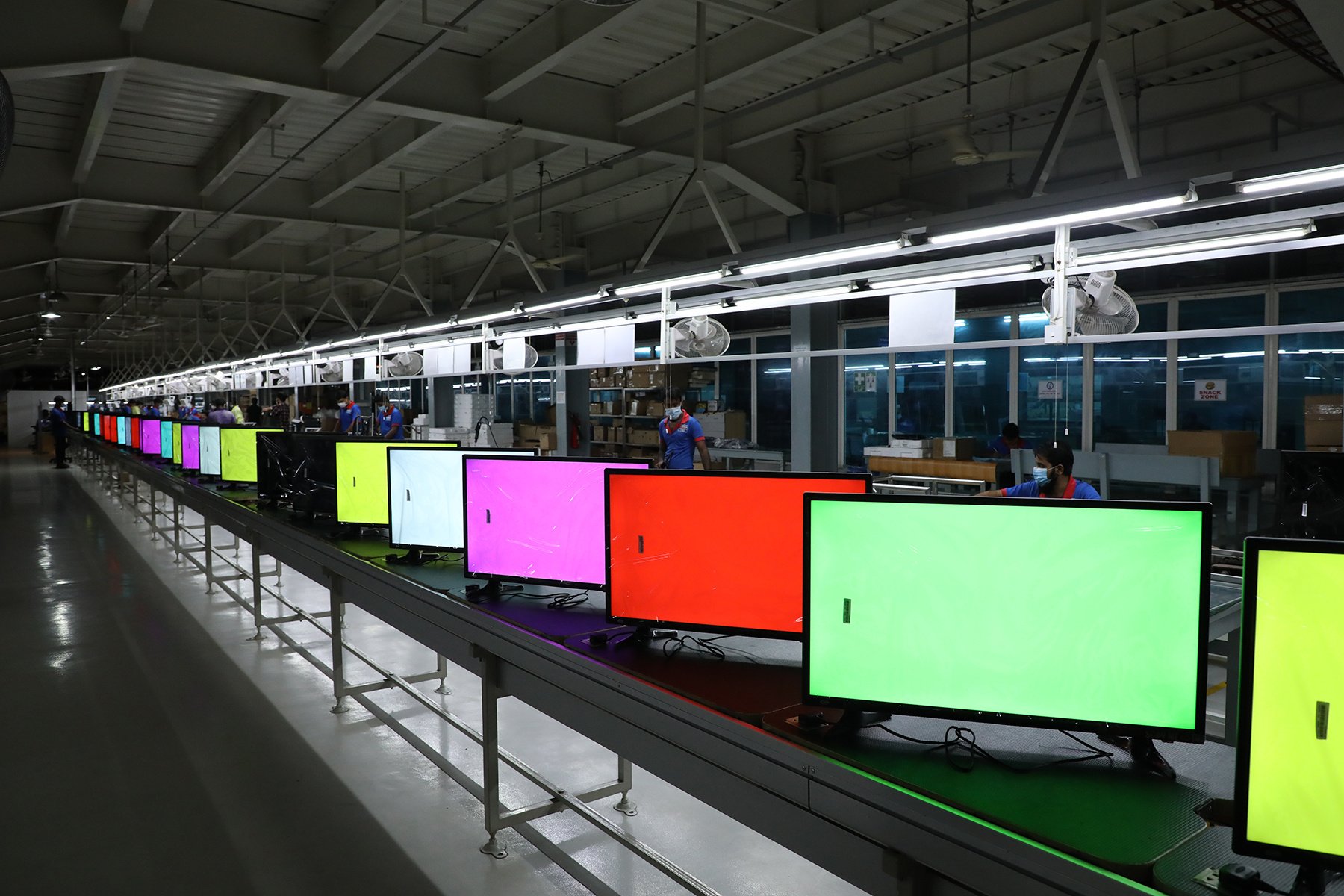
The evolution of LCD technology has enabled businesses to develop unique displays tailored to their needs. Custom display designs enhance functionality and user experience across various industries, from industrial equipment to specialized electronics. These displays are built for specific applications, ensuring better durability, performance, and seamless integration. But how do these designs transition from an idea to a final product? The journey involves multiple stages, each requiring expertise and precision. Let’s learn about the steps one by one.
The Design Phase
Every custom LCD design begins with a concept. Businesses outline their requirements, including display size, resolution, power efficiency, and durability. Engineers collaborate with clients to define specifications that align with the intended application. A well-structured design phase minimizes costly modifications later in development.
Key considerations in this phase include:- Screen type: Monochrome, TFT, OLED, or e-paper
- Brightness and contrast: Adjusted for indoor or outdoor use
- Touch integration: Capacitive or resistive touchscreens
- Power consumption: Optimized for battery or wired operation
- Viewing angles: Critical for signage, industrial screens, and automotive displays
Effective display design services ensure that all factors are accounted for before moving on to the engineering stage.
Engineering and Development
Once the design is finalized, engineers refine the product to create functional blueprints. This phase includes selecting the right components, designing circuit layouts, and optimizing power efficiency. Ensuring compatibility with existing hardware and software systems is crucial to seamless integration. Engineers also conduct thorough assessments to identify and resolve any misalignment between software and display hardware, as such issues can impact performance.
Key engineering aspects include:- Material selection: Choosing the right glass type, polarizers, and coatings for durability and visibility
- Interface compatibility: Ensuring seamless integration with HDMI, LVDS, SPI, or other custom interfaces
- Environmental factors: Designing the display to withstand temperature changes, moisture, and shock
The goal is to develop a well-balanced display that meets both technical and aesthetic requirements.
Prototyping and Testing
Prototyping is a critical step that validates design specifications before mass production begins. Rigorous testing ensures that the display meets operational requirements and industry standards.
Testing focuses on:- Visual inspection: Evaluating color accuracy, brightness, and contrast to maintain display quality
- Touch detection accuracy: Ensuring smooth and responsive touchscreen interaction
- Durability assessments: Testing resistance to shock, vibration, and environmental stress factors
- Energy efficiency: Optimizing power consumption to extend battery life and reduce operational costs
If issues are identified, engineers refine the design to enhance performance and reliability. Prototyping helps eliminate defects before full-scale production, ensuring a high-quality final product.
Manufacturing and Deployment
Once the prototype is approved, full-scale manufacturing begins. This stage involves sourcing materials, assembling components, and conducting rigorous quality control checks. Manufacturers prioritize precision and consistency to ensure that each display meets the required specifications.
Key manufacturing steps include:- Automated assembly: Enhancing production efficiency and minimizing errors
- Quality control inspections: Ensuring displays adhere to industry and client standards
- Packaging and logistics: Securely packaging displays to prevent damage during transportation
After production, the displays are deployed in their intended applications, whether in industrial settings, consumer electronics, or specialized equipment. Successful integration ensures long-term reliability and optimal performance.
Bringing a custom LCD design from concept to reality requires expertise in engineering, manufacturing, testing, and strategic planning. Businesses that invest in custom displays benefit from tailored solutions that enhance usability, efficiency, and durability. Whether developing displays for medical devices, retail kiosks, or automotive applications, expert display design services play a crucial role in delivering high-quality, application-specific solutions. By combining innovative engineering with precision manufacturing, businesses receive displays that meet their exact needs. Ready to create a custom LCD solution for your business? Contact us today to get started!
Recent Blogs
-
April 03, 2025